Why Shimming in Peristaltic Pumps?
Peristaltic pumps rely on rollers or shoes to compress and release a hose in a controlled manner, creating a vacuum that draws fluid through the system. Shimming—the process of adding or adjusting thin strips of material (shims) to fine-tune pressure control—is critical for ensuring proper hose closure, especially in pumps that use rubber hoses.
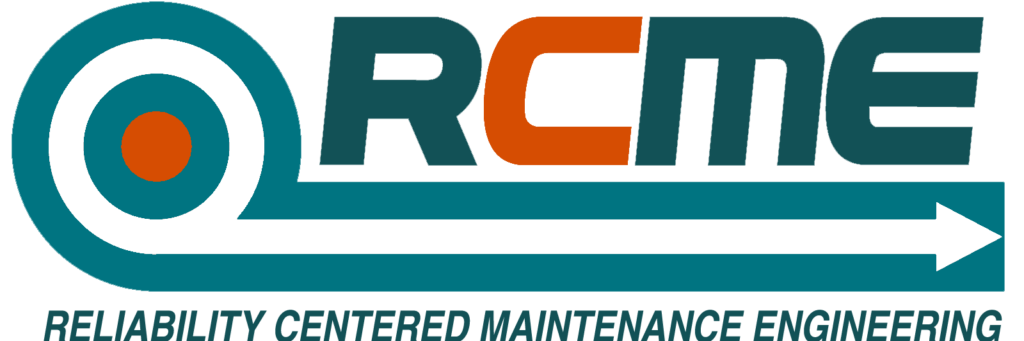
This website is proudly managed by RCME SL, your trusted partner in Peristaltic Hoses.
Why Is Shimming Necessary?
- Compensating for Manufacturing Variations
Even with precise manufacturing, slight variations in the dimensions and geometry of pump components—such as rollers, shoes, and housing—can occur. Without proper shimming, these differences can lead to uneven hose compression, reducing efficiency and hose lifespan. - Addressing Hose Material Variability
Rubber hoses, even from the same manufacturer, can have slight differences in thickness, flexibility, and resilience. These variations affect how the hose compresses under the rollers or shoes. Shimming allows fine-tuning to ensure uniform compression, optimizing pump performance. - Accounting for Thermal Expansion
During operation, components of the pump—such as the housing, rollers, shoes, and hose—expand or contract due to temperature fluctuations. These changes can alter the gap between the hose and the rollers/shoes, leading to inconsistent compression. Proper shimming compensates for these variations, maintaining reliable operation. - Ensuring Optimal Performance Across All Conditions
Shimming adjustments are typically made during setup or maintenance to maintain efficiency across different operating conditions. At various pump speeds and discharge pressures, shims help ensure that the shoes or rollers compress the hose correctly, preventing backflow or slippage.
The Impact of Correct Shimming
Proper shimming ensures that the hose is fully compressed with every revolution, maintaining the peristaltic action that moves fluid efficiently through the system. This not only enhances performance and flow consistency but also extends hose life, reducing maintenance costs and downtime.
By implementing precise shimming practices, operators can maximize pump efficiency, improve reliability, and ensure consistent, trouble-free operation.
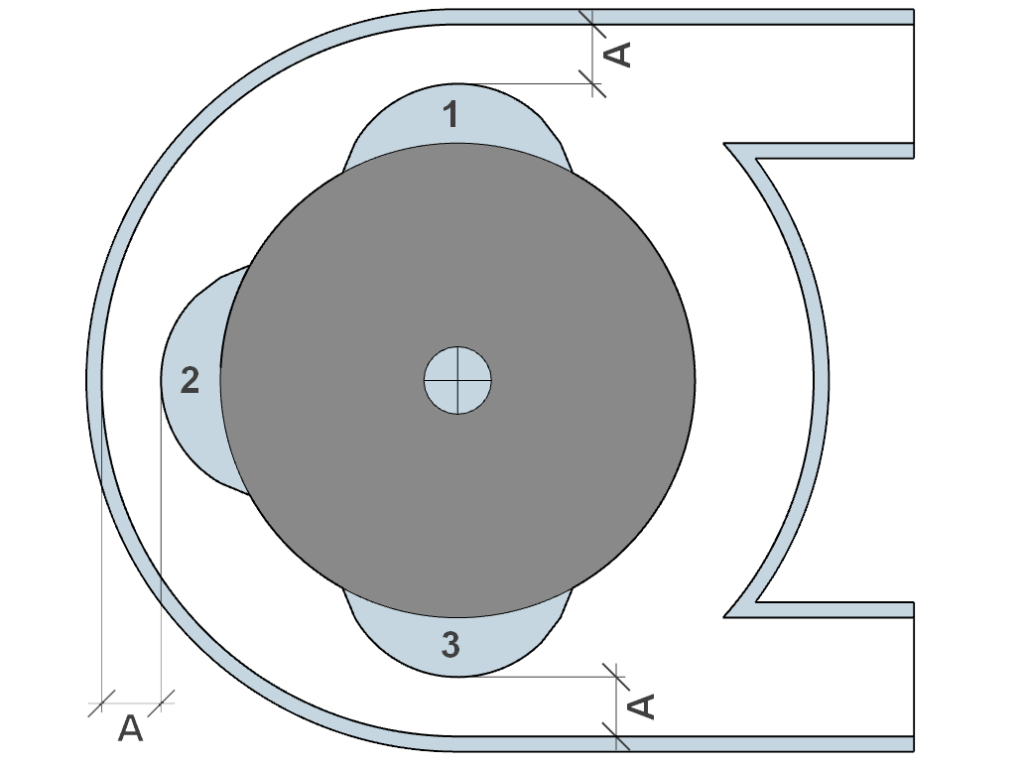
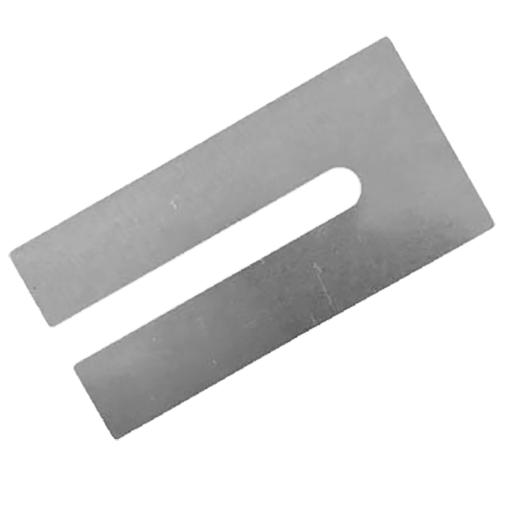
Proper Hose Installation & Shimming Guide
Correctly installing a peristaltic pump hose includes proper shimming. Follow these steps for accurate and easy shimming adjustments.
1. Measure Critical Tolerances
- Measure the A Dimension (the gap between the rotor and pump housing) at three different locations and use the largest value.
- Consider variations in hose thickness, pump housing, rotor, and pressing shoe/roller tolerances when selecting shims.
2. Check the Hose Type
- Wrapped hoses vs. Rectified hoses require different shimming levels—check your hose type before installing.
- Always measure the internal diameter (ID) of the replacement hose, as slight variations can affect compression.
3. Consider Temperature Effects
- If transferring warm or hot fluids, the hose material expands—reduce shimming by one shim to compensate.
4. Adjust for Pump Speed & Pressure
- Pump speed affects pressure: Different speeds may require different shimming adjustments. Always verify shims at different speeds and pressures.
- Calculate ΔP (pressure difference):
ΔP = Discharge Pressure – Suction Pressure
Ensure shims are adjusted based on peak pulsation pressures at both the inlet and outlet.
Pulsation Pressure Formula
For both inlet and discharge pulsation pressure, use:

Where:
- Flow = Flow rate in liters per hour (L/hr)
- Pipeline Length = Actual pipeline length in meters (m)
- S.G. = Specific Gravity of the transferred fluid
- Pump RPM = Pump head rotation speed in revolutions per minute
- Pipeline Diameter = Internal pipeline diameter in millimeters (mm)
5. Consider Fluid Viscosity
- High-viscosity fluids create more resistance, reducing backflow risk. In such cases, reduce shimming by one shim to prevent excessive compression.
6. Final Shimming Calculation
- Shims are calculated per roller/shoe. Multiply the required shims by the total number of rollers/shoes in your pump.